Understanding some of the metallurgical considerations associated with various metals
aids in the laser welding process
Laser beam welding is a fusion joining
process that uses the energy from a laser beam to melt and subsequently
crystallize a metal, resulting in a bond between parts. Laser beam welding can
be successfully used to join many metals to themselves as well as to dissimilar
metals. Main applications are related to welding steels, titanium, and nickel alloys.
Laser welding of steels
Low-carbon steels are readily laser weldable provided
that sulfur and phosphorus levels
are kept below 0.04%. A higher content can promote solidification cracking. In
low-carbon steel the welding zone is martensitic and
exhibits increased hardness, the level of which depends upon carbon and
alloying elements contents. The structure of the heat-affected zone depends
upon initial material state. In the case of annealed (normalized) condition
there is fine martensite in the place of former pearlite grains and conserved ferrite colonies, appearing
as if austenite transformation occurs separately in these two locations. This
is due to the typically short thermal cycle of laser welding and lack of time
for carbon diffusion to occur throughout the whole material. However, time is
enough for carbon redistribution to proceed in pearlite
that results in martensite formation with eutectoid
carbon content upon cooling.
The heat-affected zone in steel after
standard heat treatment (quenching and tempering) consists of two areas: a
re-quenching zone and a tempering zone. In the first area tempered martensite undergoes reverse martensite
transformation when heating up and martensite
transformation upon cooling that results in increased hardness. In the
tempering zone, temperature is not high enough for austenization,
and additional tempering proceeds.
Knowing these metallurgical features
is essential for choosing correct welding parameters and materials. At Alabama
Laser (Munford, AL)
lever-shaft assemblies made of A36 and C1018 have been successfully welded (see
Figure 1). A circumferencial butt weld 3 mm deep was
made with 2 kW power providing 30 inches/min welding speed. At the weld end the
welding head was gradually retracted so as to move the focal point above the
surface to prevent sudden collapse of a keyhole and associated weld defects.
Another example is laser welding cylindrical corrosion probe assemblies made of
C1010.
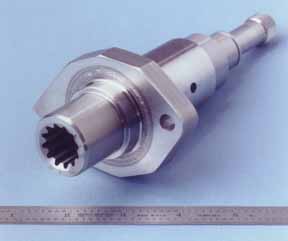
Figure 1. Laser welded lever shaft assembly composed
of two steels.
As carbon content in steel increases, martensite created in the weld zone, as well as in
heat-affected zone, becomes more brittle. Reduced toughness combined with a
high level of residual stress may lead to cracking in the weld or heat-affected
zone, and also have an adverse effect on weld embrittlement
and other alloying elements.
When the carbon equivalent is less
than 0.4, steel is readily weldable, but when it
exceeds this value, special precautions should be taken, for example,
pre-heating and/or use of filler material to change the metallurgy of the weld.
Often pre-heating is a preferred method, because it affects not only the weld
zone but also the heat-affected zone. Pre-heating can be performed with the use
of an induction heater, hot air blast, or auxiliary laser beam. Pre-heating
reduces the cooling rate, resulting in a formation of different phases other
than martensite (bainite, pearlite) that eliminates
cracking. There are no ready-to-use recipes on pre-heating temperature and
dwell time. They are dependent on the material to be welded, part geometry, and
mass. Proper choice of pre-heating and welding regimes requires experimentation.
Stainless steel
Austenitic stainless steels are good candidates for laser welding if their
sulfur and phosphor contents are kept low. Specific laser beam welding
features, such as high welding speed, small heat-affected zone, and low material
exposure at elevated temperatures are beneficial for welding this type of
steel, because prolonged periods at high temperatures may lead to chromium
precipitation on grain boundaries and reduction of corrosion resistance.
Alabama Laser has a great deal of experience in laser welding different grades
of austenitic stainless steel: 304, 316L, 309, which are used for corrosion
probes.
Martensitic stainless steels produce relatively brittle
welds due to their high carbon content. To avoid cracking, the same measures
used for high carbon steels may be performed; pre-heating and use of filler
material (in particular, austenitic wire or powder).
Alabama Laser has designed a precision
micro-wire feeder that assures full control over the wire feeding process. When
utilizing wire feeding, the wire diameter should be smaller than the size of
the weld pool (1 mm) and directed precisely into the weld. The correct wire
feed rate is determined by the gap, wire cross section, and required welding
speed.
Normal practice is to deliver the wire
at a 45° angle, intersecting the surface slightly ahead of the laser beam thus
preventing excessive spatter.
Powder feeding has an advantage
because more alloys are available than with wire. However, obtaining a constant
mass flow rate of powder over time is a problem. Selection of the method of
material delivery to the weld joint depends upon the specific task to be
performed and available resources.
Nickel alloys
Nickel and its alloys are widely used in industry due to their corrosion, heat,
and creep resistance. There are two major types of nickel alloys, solid
solution and precipitation hardenable.
The solid solution type is readily weldable with conventional methods as well as with laser
welding. Alabama Laser has welded a number of corrosion probes made of
solid-solution-type alloys (Monel 400, Inconel 600, 825) as well as heat exchanger fin assemblies
of Monel 400.
The precipitation-hardenable
type is generally difficult to weld due to cracking. Strain-age cracking can occur
under some combinations of temperature and stresses in the heat-affected zone
during or after welding. Alloys of the Nb-Al-Ti
system are generally less susceptible to this type of cracking.
Some tips on laser welding of
precipitation hardenable alloys include proper fit-up
and attention to start and closeout of the weld. If post-welding heat treatment
is necessary, weldments should be annealed first.
Also helpful are a good inert gas shield and a convex bead shape.
Titanium alloys
Titanium alloys are widely used in welded structures due to their high specific
strength and corrosion resistance. The main difficulties in welding titanium
alloys are high reactivity with gases
at elevated temperatures, especially in liquid state, that produce weld
embrittlement, and rapid grain growth at elevated
temperatures. The second drawback is easily overcome with laser beam welding,
because high welding speed and temperature gradients lead to a short material
exposure to elevated temperatures in a narrow heat-affected zone and suppressed
grain growth.
Special precautions should be taken to
protect the titanium weld area from the ambient atmosphere, including the use
of welding grade argon or argon-helium mixture as a shield gas and the use of trailing and back-up shields. The
function of trailing and back-up shield coverage is to shroud the weld and
adjacent hot material with inert gas until the surface temperature cools to
300°-400°C. Dendrite structure of the weld zone in a cross section is a good
indication of improper shielding.
The weld structure of titanium alloys
consists generally of a’ martensite, which differs
from martensite in steels by its higher toughness and
lower susceptibility to cracking. Short thermal cycles in laser welding
accounts for smaller a’ martensite needles as
compared to arc welding and, consequently, enhanced mechanical properties. A
distinctive feature of laser beam welding of titanium alloys is a very small
heat-affected zone. This is due to a low diffusion rate of a’ stabilizing elements
as compared to a carbon diffusion rate in steels.
Another factor, which has a major
impact on mechanical properties of the weld, is its chemical composition. A
number of publications indicate the superiority of laser welding over the
electron beam and arc welding with regard to fatigue strength. Laser welding is
considered superior because of its typical short welding cycle, which causes
little or no evaporation of the alloying elements.
Dissimilar metals
When welding dissimilar metals certain considerations with regard to their
properties must be taken into account; difference in melting point, heat
conductivity, reflectivity, possible formation of brittle phases, and wettability. To achieve better welding performance the laser beam can be shifted towards the
material with higher melting point, heat conductivity, and reflectivity.
A number of projects related to laser
welding of dissimilar metal have been accomplished at Alabama Laser. The most
significant is the laser welding of wear-resistant nose tips to steel guide
bars of chain saw blades for Sandvik Windsor
Corporation (see Figure 2). Previously an oxyacetylene process was used to
deposit a layer of Stellite 6 on the surface of the
steel. This process was labor intensive, hazardous, led to excessive waste of
expensive Stellite 6, and required extensive
post-welding machining operations. Laser welding of Stellite
6 tips to steel bars produced sound welds. Laser welding has many benefits; the
manufacturing environment is safer because of significant reduction of
subsequent grinding, productivity is increased by eliminating the need to
pre-heat and post-weld cool, the fusion bonding achieved with laser welding
between the Stellite and the steel bar has excellent
resistance to mechanical and thermal shock.
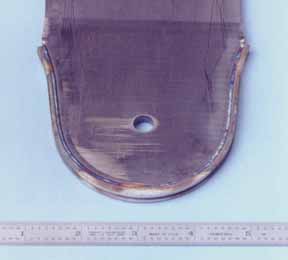
Figure 2. Wear-resistant alloy welded to chain saw
blade.
Conclusion
Laser beam welding opens up many opportunities for designing and economically
joining machine parts. Various branches of industry, which use laser beam
welding include electronics, automotive, and food processing.
Don Johnson, Wayne Penn, Sergey Bushik
|